Metal Injection Molding
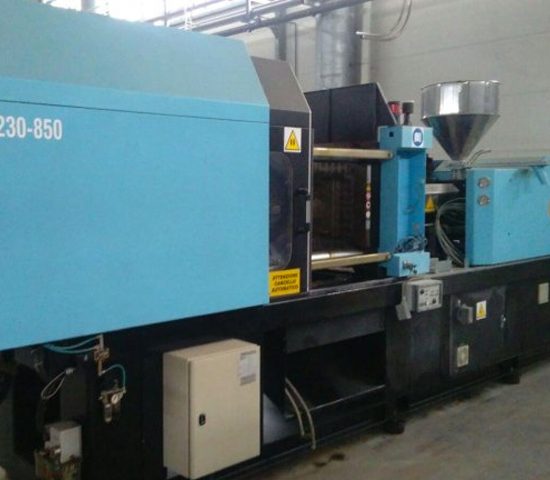
Metal injection molding is really a powder metallurgy process employed for manufacturing metal parts. Although metal injection molding uses powder metal, it's nothing beats conventional powder metal vendita presse usate sunimoto demag. The metal powders utilized in metal injection molding are 10-100 occasions smaller sized compared to powder metal processes. Also, the end result of metal injection molding is a lot greater in density. Metal injection molding provides the same features and benefits as plastic and rubber molding, but creates a much more powerful end result. Applications for metal injection molding parts include surgical tools, automotive locks and actuators, gun components, computer hard disks and electrical connectors.
Procedure For Metal Injection Molding
Metal injection molding is really a fast growing manufacturing way in which bridges the space between your technology up gradation and charges involved. The metal injection molding process involves five steps, mixing, injection molding, de binding, sintering, and part finishing.
Within the mixing step, metallic powders, selected for his or her strengths and natural abilities for example impact strength, everywhere temperature characteristics, put on resistance characteristics, machine ability, and hardness, are mixed, frequently having a binding agent. By mixing powders, the aim is to produce a composite using the strengths and benefits of all of the incorporated metals, while offsetting the independent weaknesses.
When the powders are mixed, a "feedstock" is created. This feedstock is injected into molds in the same manner that plastic or rubber injection molding is conducted. The part that emerges in the injection molding stage is called a "eco-friendly" part.
Within the de binding stage of metal injection molding, the eco-friendly part is immersed inside a water bath to get rid of the binder, that has joined in to the part matrix. In mix-linking, the de bound eco-friendly part is uncovered to ultraviolet light which thermo sets the binding agents combined with the metal powders.
When the de binding stage continues to be completed, the part is positioned right into a furnace and heated to in excess of 2000 degree F. This method, known as sintering, fuses the metal parts right into a solid shape. Finally, the sintered piece is distributed to some finished stage where burrs and surface imperfections are removed and also the finished part could be shipped.
Purposes Of Metal Injection Molding
We've got the technology excels at applications that need shape complexity and final qualities, for example high strength and density, excellent magnetic permeability, hot temperature strength, corrosion resistance, and thermal conductivity in applications that can't be satisfied by plastics or light metal alloys. Metal injection molding is thus perfect for a few of the following uses viz. making of microelectronic packaging, automotive sensors and actuators, hands tools and hardware, computer heat dissipation devices, oil well drilling tools, aerospace and engine fuel components.
To Summarize
Metal injection molding can offer a considerable financial savings over conventional metal machining options. Metal injection molding parts have high densities and mechanical qualities approaching individuals of forged or machined components. Metal injection molding process can establish more complicated parts than either investment casting or traditional press and sinter techniques.